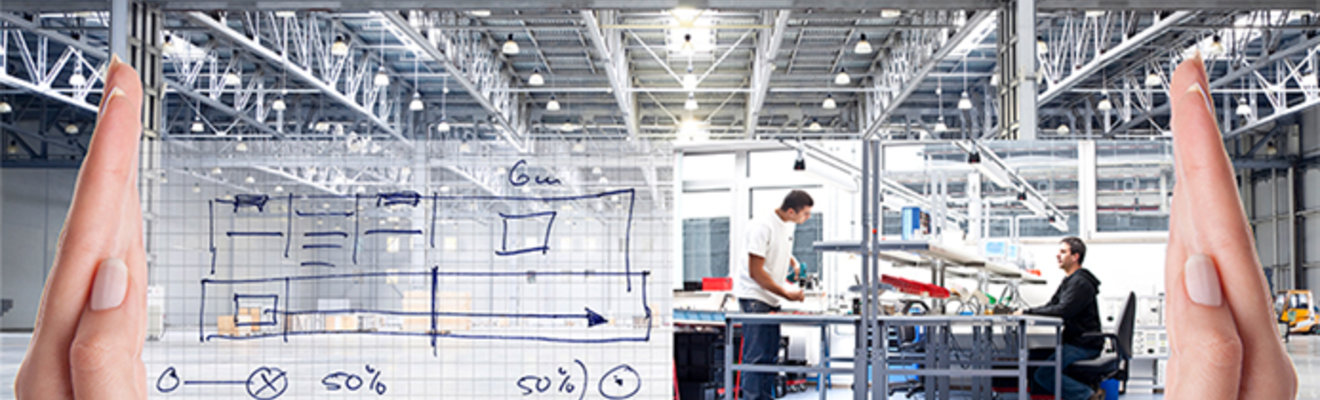
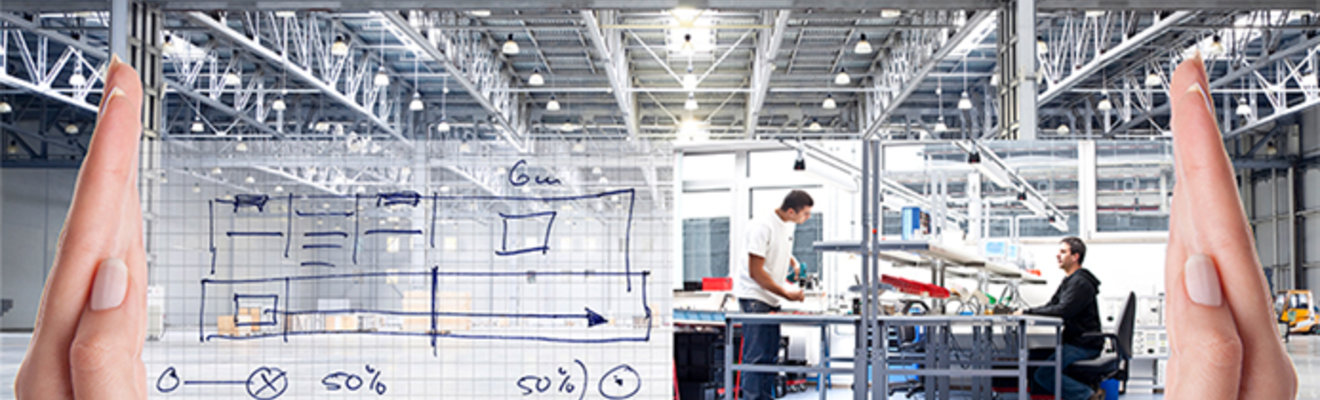
What Is Lean Manufacturing Process?
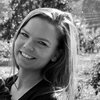
Carissa Harris
To reduce the mentality behind lean production to a single phrase, reflect on an observation made by Shigeo Shingo, one architect of TPS: “Only the last turn of a bolt tightens it—the rest is just movement.”
What Are The Goals Of Lean Production?
The main purpose of lean production is to eliminate waste while producing a high-quality product. Waste, however, is a broad concept that refers to a range of types of waste. These include:
-
Unnecessary transportation
-
Standing inventory
-
Unnecessary movement
-
Waiting
-
Overproduction
-
Overprocessing
-
Defects
How Do You Identify and Approach Productivity Waste?
Facilities that use lean processes employ a principle of continuous improvement (also known as kaizen) to seek opportunities for improvement. Seeking continual improvement in all processes compliments seeking to eliminate waste from every step of each process. Documenting and managing all processes and procedures will help achieve improvements.
Respecting the human element of the manufacturing process is a key part of the lean process. Not overworking employees, ensuring they understand the purpose of their work and aligning it with their goals, minimizing things that would prevent employees from completing their tasks, promoting stability, and encouraging communication are all parts of a successful lean work environment.
Mistake proofing (also known as poka yoke) is a key element for building quality into lean manufacturing processes. Poka yoke seeks to either create specific measures to ensure mistakes are caught early when they can still be corrected, or to reactively re-engineer tasks in such a way that mistakes are being inherently prevented as part of the process.
What Are The Steps Of Lean Cycle?
The lean process creates a self-driving cycle. Being committed to pursuing the perfect process involves seeking continuous improvement at all steps along the way. The five steps of a lean cycle are:
-
Identify what the customer values in the final product
-
Remove any steps during the manufacturing process that do not add value
-
Streamline the production process so that steps occur as sequentially as possible
-
Create customer pull and develop production methods around that rather than pushing products onto customers
-
Critically examine every step and stage of your production process and identify ways to improve it via eliminating waste
What Are The Benefits Of Lean Production?
Lean production processes seek to help businesses save money and make the most of their resources by minimizing waste and only producing as much as they need. The lean process encourages a just-in-time process that is dictated by customer pull rather than push.
JIT manufacturing involves working on a task or item in order to meet demand and nothing beyond that. This way, it produces no standing inventory. However, JIT has inherent difficulties because if a hurdle appears at any point during the process, then order fulfillment will be delayed until that obstacle is removed. These obstacles can range from equipment malfunctioning to employee output decreases due to fatigue.
A common way to construct a modern learn production queue is to establish a one piece flow process.
What is The One Piece Flow Process?
One piece flow is the lean manufacturing process in which WIP is limited to a single item with the intent to increase the efficiency and quality of the finished product. One piece flow production lines have several workstations that move an item from one workstation to the next as work is completed at each. After an item is moved from one station to the next, the next item in the queue then moves onto the first workstation so that the items are completed sequentially with as little time between tasks as possible. This allows for quality to be built into the process, minimizing errors and completing repetitive tasks faster and with higher quality.
How Do I Set Up An Ideal Lean Production Line?
A production line’s design can make or break its success. To maximize efficiency in your production line, you have to first take into consideration the human element of which. Ergonomic workstations increase productivity and quality by reducing fatigue by eliminating unnecessary movement. Comfortable, adjustable chairs allow users to work at high levels of productivity for sustained periods of time. Modular furniture allows for each space to be configured for the exact type of work and the physiological needs of the user.
Modular workstations are those that can be customized to fit the needs of the type of work being done and the preferences of the user. Treston offers a variety of industrial workbenches suited for a range of manual assembly workspaces, including electronics, labs, and defense.
Our Concept workbench is our most customizable workbench. Add upright frames that can be equipped with perforated panels, shelves, drawers, bin rails, and more. The Concept workbench emphasized ergonomics with electric motor-driven height adjustability, multiple work surface material options, and an option for ESD protection.
We also have Cornerstone workbenches that can be customized with a variety of accessories to meet the needs of any assembly station.
Customize Your Workspace for Lean Production with Treston
Want to learn more about how to implement the lean process in your assembly facility? Contact the experts at Treston who will consult with you on creating the ideal ergonomic workstation that will help your operation by reducing waste and consistently producing a high-quality product. If you want to customize your space with a visual online tool, then look to our 3D Configurator, a free experience for you to build and document exactly what you need for your workspace.